Quality, according to Juran,
means that a product meets customer needs leading to customer satisfaction, and
quality also means all the activities in which a business engages in to ensure
that the product meets customer needs.
Major
contributions of Joseph Juran are:
- Juran’s Trilogy
- Cost of Quality
- Juran’s 10 steps to quality improvement
Juran’s
Trilogy
Juran was one of the
first to write about the cost of poor quality. Juran’s Trilogy is an approach to
cross functional management that is composed of three managerial processes:
planning, control, and improvement. Quality planning is all about developing
methods to stay in tune with customer’s expectations. Quality control involves
checking the products produced with specifications. Quality improvement involves
the continuous business process improvement.10
- Quality Planning: This is the activity of developing the products and processes required to meet customer’s needs. It involves a series of universal steps which can be abbreviated as follows:
a. Establish
quality goals
b. Identify
the customers- those who will be impacted by the efforts to meet the goal.
c. Determine
the customers’ needs
d. Develop
product features that respond to customers’ needs
e. Develop
processes that are able to produce those product features
f. Establish
process controls, and transfer the resulting plans to the operating forces
- Quality Control: This process consists of the following steps:
a. Evaluate
actual quality performance
b. Compare
actual performance to quality goals
c. Act on the
difference11
- Quality Improvement: This process is the means of raising quality performance to unprecedented levels (“breakthrough”). The methodology consists of a series of universal steps:
a. Establish
the infrastructure needed to secure annual quality improvement.
b. Identify
the specific needs for improvement -the improvement projects
c. For each
project establish a project team with clear responsibility for bringing the
project to a successful conclusion
d. Provide the
resource, motivation, and training needed by the team to:
e. Diagnose
the cause
f. Stimulate
establishment of remedies
g. Establish
controls to hold the gains12
Cost of Quality
Cost of Quality (COQ) is
regarded as an important QM technique which measures the cost incurred in
achieving better and improved product or service quality.13
- Prevention Costs: The costs of all activities specifically designed to prevent poor quality in products or services. Examples are the costs of:
·
New product review
·
Quality planning
·
Supplier capability surveys
·
Process capability evaluations
·
Quality improvement team meetings
- Appraisal Costs: The costs associated with measuring, evaluating or auditing products or services to assure conformance to quality standards and performance requirements. These include costs of:
·
Incoming and source inspection/test of purchased
material
·
In-process and final inspection/test
·
Product, process or service audits
·
Calibration
of measuring and test equipment
·
Associated
supplies and materials
- Failure Costs: The costs resulting from products or services not conforming to requirements or customer/user needs. Failure costs are divided into internal and external failure categories.
- Internal Failure Costs: Failure costs occurring prior to delivery or shipment of the product, or the furnishing of a service, to the customer.
o
Scrap
o
Rework
o
Re-inspection
o
Re-testing
- External Failure Costs: Failure costs occurring after delivery or shipment of the product — and during or after furnishing of a service — to the customer. Examples are the costs of:
o
Processing customer complaints
o
Warranty
claims
o
Product
recalls
o
Customer returns 14
Juran’s
10 steps to quality improvement
Juran believed quality
is associated with customer satisfaction and dissatisfaction with the product,
and emphasized the necessity for ongoing quality improvement through a
succession of small improvement projects carried out throughout the
organization.15 His ten steps to quality improvement are:
• Build awareness of the need and opportunity for
improvement
• Set goals for improvement
• Organize to reach the goals
• Provide training
• Carry out projects to solve problems
• Report progress
• Give recognition
• Communicate results
• Keep score of improvements achieved
• Maintain
momentum by making annual improvement part of the regular systems and processes
of the company
References
8. Phillips-Donaldson, Debbie (May 2004), "100 Years Of Juran", Quality Progress (Milwaukee, Wisconsin: American Society for Quality) 37 (5): PP:25–39
9. http://www.juran.com/juran-international/
10. Gupta, Total Quality Mgmt, 2E, Tata McGraw-Hill Education, New Delhi, 2009, Pg:42
11. J.M. Juran, Juran on Planning for Quality, The Free Press, New York, pp. 11-12.
12. Joseph Juran, http://www.qualitygurus.com/gurus/list-of-gurus/joseph-juran/
13. J. J. Plunkett & B. G. Dale, Quality costs: a critique of some ‘economic cost of quality’ models, International Journal of Production Research, Volume 26, Issue 11, 1988, PP 2-3
14. Cost of Quality, http://asq.org/learn-about-quality/cost-of-quality/overview/overview.html
15. Juran’s 10 Steps to Quality Improvement, http://www.5squalityposters.com/blog/?p=99
9. http://www.juran.com/juran-international/
10. Gupta, Total Quality Mgmt, 2E, Tata McGraw-Hill Education, New Delhi, 2009, Pg:42
11. J.M. Juran, Juran on Planning for Quality, The Free Press, New York, pp. 11-12.
12. Joseph Juran, http://www.qualitygurus.com/gurus/list-of-gurus/joseph-juran/
13. J. J. Plunkett & B. G. Dale, Quality costs: a critique of some ‘economic cost of quality’ models, International Journal of Production Research, Volume 26, Issue 11, 1988, PP 2-3
14. Cost of Quality, http://asq.org/learn-about-quality/cost-of-quality/overview/overview.html
15. Juran’s 10 Steps to Quality Improvement, http://www.5squalityposters.com/blog/?p=99
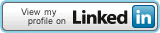
Thanks for sharing superb informations. Your web site is so cool. I’m impressed by the details that you have on this website. It reveals how nicely you understand this subject. Bookmarked this website page, will come back for extra articles. You, my pal, ROCK! I found simply the information I already searched all over the place and just couldn’t come across. What a great web site. Manila Inspection Company
ReplyDeleteAcknowledges for paper such a beneficial composition, I stumbled beside your blog besides decipher a limited announce. I want your technique of inscription... Construction Management
ReplyDelete