After a
number of years in industry, Crosby established the Crosby Quality College in
Winter Park, Florida. He is well known as an author and consultant and has
written many articles and books. He is probably best known for his book Quality
is Free (1979) and concepts such as his Absolutes of Quality Management,
Zero Defects, Quality Management Maturity Grid, 14 Quality Improvement Steps,
Cost of Quality, and Cost of Nonconformance. Other books he has
written include Quality Without Tears (1984) and Completeness (1994).2
Major contributions of Philip
Crosby are:
- Crosby’s Cost of Quality
- Four Absolutes of Quality
- The Fourteen Steps to Quality Improvement
- The Crosby Vaccine
Crosby's Concept Of Cost Of Quality
In his book
Quality Is Free, Crosby makes the point that it costs money to achieve quality,
but it costs more money when quality is not achieved. When an organization
designs and builds an item right the first time, quality is free. It does not
cost anything above what would have already been spent. When an organization
has to rework or scrap an item because of poor quality, it costs more. Crosby
notes that most companies spend 15 to 20 percent of their sales dollars on quality
costs. Accompany with a well-run quality management program can achieve a cost
of quality that is less than 2.5 percent of sales, primarily in the prevention
and appraisal categories.17
Four Absolutes of Quality
Crosby defines
four absolutes of quality:
- The definition of quality is conformance to requirements
- The system of quality is prevention
- The performance standard is zero defects
- The measurement of quality is the price of nonconformance18
To support his Four
Absolutes of Quality Management, Crosby developed the Quality Management
Maturity Grid and Fourteen Steps of Quality Improvement. Crosby sees the Quality
Management Maturity Grid as a first step in moving an organization towards
quality management. After a company has located its position on the grid, it
implements a quality improvement system based on Crosby's Fourteen Steps of
Quality Improvement.2
The Fourteen Steps to Quality Improvement
The 14 Steps of Crosby formulate
a program for Total Quality Management efforts. Crosby's fourteen steps rely on
the foundational thought that any money a company spends upon quality
improvement is money that is well-spent.19
- Management is committed to quality – and this is clear to all: Clarify where management stands on quality. It is necessary to consistently produce conforming products and services at the optimum price.
- Create quality improvement teams – with representatives from all workgroups and functions: These teams run the quality improvement program. Since every function of an operation contributes to defect levels, every function must participate in the quality improvement effort.
- Measure processes to determine current and potential quality issues: Communicate current and potential non-conformance problems in a manner that permits objective evaluation and corrective action. Basic quality measurement data is obtained from the inspection and test reports, which are broken down by operating areas of the plant. It should be mentioned that unless this data is reported properly, it is useless.
- Calculate the cost of (poor) quality: Define the ingredients of the COQ and explain its use as a management tool.
- Raise quality awareness of all employees: Provide a method of raising the personal concern felt by all personnel in the company toward the conformance of the product or service and the quality reputation of the company.
- Take actions to correct quality issues: Provide a systematic method of permanently resolving the problems that are identified through previous action steps. Problems that are identified during the acceptance operation or by some other means must be documented and then resolved formally.
- Monitor progress of quality improvement – establish a zero defects committee: Examine the various activities that must be conducted in preparation for formally launching the Zero Defects program - The quality improvement task team should list all the individual action steps that build up to Zero Defects day in order to make the most meaningful presentation of the concept and action plan to personnel of the company.
- Train supervisors in quality improvement: Define the type of training supervisors need in order to actively carry out their part of the quality improvement program. The supervisor, from the board chairman down, is the key to achieving improvement goals. Therefore, the supervisor must be given primary consideration when laying out the program.
- Hold zero defects days: Create an event that will let all employees realize through personal experience, that there has been a change. Zero Defects is a revelation to all involved that they are embarking on a new way of corporate life. Working under this discipline requires personal commitments and understanding.
- Encourage employees to create their own quality improvement goals: Turn pledges and commitments into action by encouraging individuals to establish improvement goals for themselves and their groups.
- Encourage employee communication with management about obstacles to quality (Error-Cause Removal): Give the individual employee a method of communicating to management the situations that make it difficult for the employee to fulfill the pledge to improve. One of the most difficult problems employees face is their inability to communicate problems to management.
- Recognize participants’ effort: Appreciate those who participate. People really don’t work for money. They go to work for it, but once the salary has been established, their concern is appreciation. Recognize their contribution publicly and noisily, but don’t demean them by applying a price tag to everything.
- Create quality councils: Bring together the professional quality people for planned communication on a regular basis. It is vital for the professional quality people of an organization to meet regularly just to share their problems, feelings, and experiences, with each other
- Do it all over again – quality improvement does not end: Emphasize that the quality improvement program never ends. There is always a great sign of relief when goals are reached. If care is not taken, the entire program will end at that moment. It is necessary to construct a new quality improvement team, and to let them begin again and create their own communications.20
References
16. Wikipedia,
http://en.wikipedia.org/wiki/Philip_B._Crosby#cite_ref-4
17. Crosby’s
Cost of Quality, http://www.zeepedia.com/read.php?crosbys_concept_of_cost
_of_quality_cost_of_quality_
attitude_total_quality_management_tqm&b=59&c=17
18. Fritz E Froehlich, The Froehlich/Kent
Encyclopedia of Telecommunications, Marcel Dekker Inc, Newyork, 1995, Pg:
301
19. Ronda Bowen, 14 steps of Crosby, http://www.brighthubpm.com/methods-strategies/94048-fourteen-steps-of-crosby/
20. Philip Crosby’s concept
of Quality Improvement, http://www.qasigma.com/2008/12/philip-crosbys-concept-of-quality-improvement.html
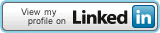
Sweet web site , super design and style , very clean and utilise pleasant. Total Quality Management partner Singapore
ReplyDeleteThis is very useful, although it will be important to help simply click that web page link: General Contractors in Canada
ReplyDelete