He wrote
647 articles and 31 books, including two that were translated into English:
Introduction to Quality Control and What Is Total Quality Control? The Japanese Way.
He is well known for coming up with the concept for the fishbone shaped diagram, known as the Ishikawa or cause and effect diagram, used to improve the performance of teams in determining potential root causes of their quality problems.22
Introduction to Quality Control and What Is Total Quality Control? The Japanese Way.
He is well known for coming up with the concept for the fishbone shaped diagram, known as the Ishikawa or cause and effect diagram, used to improve the performance of teams in determining potential root causes of their quality problems.22
Throughout
his career, Ishikawa worked on very practical matters, but always within a
larger philosophical framework. In its broadest sense, Ishikawa's work was
intended to produce what he called a "thought revolution" new ideas
about quality that could revitalize industry. The wide acceptance of many of
Ishikawa's ideas—and the numerous honors he has received from around the world
show how successful his revolution has been.23
Major contributions of Kaoru Ishikawa are:
- Ishikawa Diagram
- Seven basic quality tools
- Quality Circles
- Company-wide Quality Control
Ishikawa Diagram [Fishbone Diagram]
The
Ishikawa Diagram was developed by Kaoru Ishikawa and is by far the most popular
form of causal map. The Ishikawa Diagram is a special type of causal map that
shows the relationships between the problem and the potential causes of a
problem. It is usually developed in a brainstorming context. The process begins
by placing the name of a basic problem of interest at the far right of the
diagram at the “head” of the main “backbone” of the fish. The main causes of
the problem are drawn as bones off the main backbone.24
Seven Basic Quality Tools
The Seven
Basic Tools of Quality is a designation given to a fixed set of graphical
techniques identified as being most helpful in troubleshooting issues related
to quality.25 They are called basic because they are suitable
for people with little formal training in statistics and because they can be
used to solve the vast majority of quality-related issues.26
- Cause-and-effect diagram (also called Ishikawa or fishbone chart): Identifies many possible causes for an effect or problem and sorts ideas into useful categories.
- Check sheet: A structured, prepared form for collecting and analyzing data; a generic tool that can be adapted for a wide variety of purposes.
- Control charts: Graphs used to study how a process changes over time.
- Histogram: The most commonly used graph for showing frequency distributions, or how often each different value in a set of data occurs.
- Pareto chart: Shows on a bar graph which factors are more significant.
- Scatter diagram: Graphs pairs of numerical data, one variable on each axis, to look for a relationship.
- Stratification: A technique that separates data gathered from a variety of sources so that patterns can be seen (some lists replace “stratification” with “flowchart” or “run chart”).27
Quality Circles
A quality
circle is a group of workers who do the same or similar work, who meet
regularly to identify, analyze and solve work-related problems.28
Normally small in size, the group is usually led by a supervisor or manager and
presents its solutions to management; where possible, workers implement the
solutions themselves in order to improve the performance of the organization
and motivate employees. Quality circles were at their most popular during the
1980s, but continue to exist in the form of Kaizen groups and similar worker
participation schemes29.
Quality
circles are typically more formal groups. They meet regularly on company time
and are trained by competent persons (usually designated as facilitators) who
may be personnel and industrial relations specialists trained in human factors
and the basic skills of problem identification, information gathering and
analysis, basic statistics, and solution generation.30 Quality
circles are generally free to select any topic they wish (other than those
related to salary and terms and conditions of work, as there are other channels
through which these issues are usually considered).
Company-wide Quality Control
Turning to organizational, rather than technical contributions to quality, Ishikawa is
associated with the Company Wide Quality Control movement that started in Japan
in the years 1955-1960 following the visits of Deming and Juran. Under this, quality
control in Japan is characterized by company-wide participation from top
management to the lower-ranking employees. Further, all study statistical
methods. As well as participation by the engineering design, research and
manufacturing departments, also sales, materials and clerical or management
departments (such as planning, accounting, business and personnel) are
involved.31
The company-wide quality approach places an emphasis
on four aspects:-
- Elements such as controls, job management, adequate processes, performance and integrity criteria and identification of records
- Competence such as knowledge, skills, experiences, qualifications
- Soft elements, such as personnel integrity, confidence, organizational culture, motivation, team spirit and quality relationships.
- Infrastructure (as it enhances or limits functionality)
The results of these
company-wide Quality Control activities are remarkable, not only in ensuring
the quality of industrial products but also in their great contribution to the
company's overall business. Thus Ishikawa sees the Company Wide Quality Control
movement as implying that quality does not only mean the quality of product,
but also of after sales service, quality of management, the company itself and
the human being.
References
21. Wikipedia, http://en.wikipedia.org/wiki/Kaoru_Ishikawa
22. Quality Gurus, http://www.qualitygurus.com/gurus/list-of-gurus/kaoru-ishikawa/
23. Kaoru Ishikawa , http://asq.org/about-asq/who-we-are/bio_ishikawa.html
24. Arthur V. Hill, The Encyclopedia of Operations Management, Pearson Education Inc,New Jersey, 2011, Pg:63
22. Quality Gurus, http://www.qualitygurus.com/gurus/list-of-gurus/kaoru-ishikawa/
23. Kaoru Ishikawa , http://asq.org/about-asq/who-we-are/bio_ishikawa.html
24. Arthur V. Hill, The Encyclopedia of Operations Management, Pearson Education Inc,New Jersey, 2011, Pg:63
25. Montgomery, Douglas (2005). Introduction to Statistical Quality Control. Hoboken, New Jersey: John Wiley & Sons, Inc. p. 148.
26. Ishikawa, Kaoru , What Is Total Quality Control? The Japanese Way (1 ed.), Englewood Cliffs, New Jersey: Prentice-Hall, 1985, p. 198
27. Seven basic quality tools, http://asq.org/learn-about-quality/seven-basic-quality-tools/overview/overview.html
28. Wikipedia, http://en.wikipedia.org/wiki/Quality_circle
29. Edward E. Lawler III & Susan A. Mohrman, Quality Circles After the Fad, https://hbr.org/1985/01/quality-circles-after-the-fad/ar/1
30. Montana, Patrick J., Bruce H. Charnov. Management (4th ed.). Barron's, Newyork, 2008, Pg:81.
31. Kaoru Ishikawa, http://www.systemsthinking.co.uk/members/library/kaoru_ishikawa.asp
32. Cause and effect diagram, http://www.skymark.com/resources/tools/cause.asp
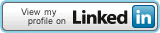
26. Ishikawa, Kaoru , What Is Total Quality Control? The Japanese Way (1 ed.), Englewood Cliffs, New Jersey: Prentice-Hall, 1985, p. 198
27. Seven basic quality tools, http://asq.org/learn-about-quality/seven-basic-quality-tools/overview/overview.html
28. Wikipedia, http://en.wikipedia.org/wiki/Quality_circle
29. Edward E. Lawler III & Susan A. Mohrman, Quality Circles After the Fad, https://hbr.org/1985/01/quality-circles-after-the-fad/ar/1
30. Montana, Patrick J., Bruce H. Charnov. Management (4th ed.). Barron's, Newyork, 2008, Pg:81.
31. Kaoru Ishikawa, http://www.systemsthinking.co.uk/members/library/kaoru_ishikawa.asp
32. Cause and effect diagram, http://www.skymark.com/resources/tools/cause.asp
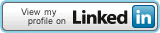
No comments:
Post a Comment